Key Takeaways:
Across almost all sectors, we are seeing a digital shift. Aptly named digital transformation, the process involves organisations readying their digitised capabilities in order to better serve themselves and their respective markets. In manufacturing, digital transformation is a large, if not the biggest, part of adopting Industry 4.0, and there is a lot to consider when starting the journey.
With a sole emphasis on digitisation, the process carries risks and challenges among its benefits. But, with good data strategies and strong cybersecurity, organisations can overcome these hurdles and fully realise themselves in a new, digital era.
Navigating the complex landscape can prove precarious, but with the right strategies and expert advice, the uncertain water can clear. RSM’s specialists in Europe discuss how manufacturers can effectively implement a robust data strategy to leverage industrial data, concerns surrounding cybersecurity, and how to overcome the challenges that come with digital transformation.
If you missed the first article in this series, be sure to find it on our manufacturing page or by following the link below:
Data’s role in the next stage of manufacturing
As stated by Götz Brinkmann, Principal at RSM Ebner Stolz, “The prerequisite for a successful Industry 4.0 roadmap is the synchronisation of business and data strategy, and the question of how existing, or yet to be generated, data should be used in a meaningful way.” Industry 4.0 is defined, in part, by its increased connectivity and digitalisation, as well as the data that comes with it all. This could be data generated by machines, software, stakeholders, clients, or any other connected devices during the manufacturing process. Without care and a sufficient data strategy, many organisations may find themselves stumped in the face of increasingly stringent regulations – let alone by competition that leverages their data for informed, data-driven decision-making.
The benefits of effectively wielding data are numerous. As Simone Segnalini, Partner - Digital, Risk and Transformation at RSM Italy, says, “Firstly, integrating Internet of Things (IoT) sensors on machines and assembly lines enables real-time monitoring of operations. This data, when analysed using AI algorithms, can predict maintenance needs, optimise production efficiency, and reduce downtime. Such proactive measures ensure more informed decision-making.”
And what about safety? Notoriously, production lines can be dangerous places if procedures and planning are not set out or appropriately properly – and there can always be unforeseen incidents. Yet, collected data can help manufacturers to bolster their safety standards and minimise risks. “More and more of our manufacturing clients are using data to enhance safety on their production lines by employing predictive analytics to forecast potential safety hazards,” says Mike Thornton, Partner and Head of Manufacturing at RSM UK. “Real-time monitoring through sensors and IoT devices can identify anomalies and trigger alerts for immediate intervention. Additionally, using historical data, like incident reports and near-miss data, is helping many identify patterns and proactively implement preventive measures.” Segnalini adds, “Additionally, integrating wearable safety devices with IoT can monitor workers' health and environmental conditions, ensuring immediate response in emergencies.”
So, what can manufacturers do to implement robust data strategies in their organisations? According to Thornton, “Establishing clear objectives aligned with business goals is always the first step when looking to implement a data strategy. Only then should manufacturers consider their investments in robust data collection tools and platforms. These must be capable of handling diverse data types coming from different machines and devices. Adopting advanced analytics and machine learning models will help derive actionable insights from this data. In the UK, we have seen some of the bigger players such as Rolls Royce utilise machine learning algorithms to predict engine maintenance needs and optimise operations more generally.”
“Ultimately,” Thornton continues, “integrating data analytics, machine learning, and real-time monitoring empowers manufacturers to not only improve operational efficiency but also prioritise safety in the production environment, a crucial aspect of Industry 4.0 adoption.”
Concerns with cybersecurity
With an increased emphasis on digitisation, data, and connected devices, it is no surprise that cybersecurity has become more important than ever. All the benefits that come with digital transformation and Industry 4.0 are only as strong and sustainable as the cybersecurity that protects them. As Segnalini says, “In Europe’s increasingly digitalised manufacturing sector, bolstering cybersecurity is crucial to protect against cyber threats in a landscape where workers, machines, and supply chains are interconnected.”
The scale and variety of cyber-related attacks have increased dramatically in recent years as people’s work lives continue to shift online. Luckily, more and more business leaders are becoming aware of cyber risks and the state of their organisations’ cybersecurity, and awareness is key to protection in the first instance. “With the increasing number of cyber-attacks, IT security should be a top management priority to protect the business from critical or even threatening consequences,” says Brinkmann. “Medium-sized companies are sometimes inadequately protected against threats, especially around industrial control systems.”
So, what can manufacturers do to mitigate the risks that come with digital transformation? According to Thornton, “For many, the place to start will be conducting comprehensive risk assessments to identify vulnerabilities across their interconnected systems. Implementing robust access controls, encryption protocols, and regular security audits can then strengthen networks and protect sensitive data. Because the cyber landscape is so fast-moving, regularly training employees on cybersecurity best practices is crucial to prevent human error-related breaches.” Segnalini adds: “Manufacturers should adopt a layered security approach, incorporating firewalls, intrusion detection systems, and regular security audits to identify vulnerabilities.”
Thornton continues, “Moreover, collaborating with supply chain partners can lead to mutual cybersecurity standard setting and continuous monitoring of shared networks. Embracing technologies like AI and machine learning for anomaly detection enhances the ability to identify and respond swiftly to potential threats, too. By prioritising cybersecurity as an integral part of their digital transformation, manufacturers can better safeguard against evolving cyber threats.”
Overcoming the hurdles of digital transformation
As manufacturers look to transition to Industry 4.0, ensuring a flexible, scalable, and highly interconnected IT architecture is critical to support their digital transformation and the shift towards more data-driven operations. However, in addition to cybersecurity, the journey has its fair share of challenges to overcome.
According to Thornton, “One of the most common challenges remains legacy system integration with existing infrastructure needing to be adapted to accommodate new digital tools. This often causes compatibility and interoperability issues that can slow down the transformation process.” He continues: “Other issues include the often-high initial costs required to drive the transformation and talent shortages for managing some of the new and more advanced technologies.” And, of course, during all of this, cybersecurity, data security, and regulatory compliance needs should all be met.
Despite challenges, there are many ways for manufacturers to stay ahead during their transition. “This involves using cloud services and edge computing to efficiently handle large data volumes, ensuring real-time data processing and analytics. Additionally, prioritising interoperability between different systems and platforms is crucial to maintain a seamless flow of information,” says Segnalini. “Training programs to upskill employees in digital competencies are also essential, fostering a culture of continuous learning and adaptation. This strategic approach will enable Italian manufacturers to effectively manage their digital transformation and leverage data-driven operations.”
There are several other strategies that manufacturers should prioritise to ensure a flexible, scalable, and interconnected IT architecture, according to Thornton. These are:
- Adopting modular and scalable solutions allows for flexibility in accommodating future technological advancements.
- Embracing cloud-based platforms can facilitate scalability by offering on-demand resources and simplifying data sharing across the organisation.
- Implementing robust API frameworks enables seamless integration between different systems and devices, fostering interoperability.
- Investing in agile methodologies and cross-functional collaboration within the organisation promotes adaptability to changing technology landscapes.
As Thornton says, “By strategically planning for scalability, fostering interoperability, and cultivating an adaptable culture, manufacturers can build a resilient IT architecture capable of supporting data-driven operations and accommodating future technological shifts.”
The takeaway
Industry 4.0 is the next natural step in the manufacturing sector’s evolution, and with that increased emphasis on digitalisation and connected devices, it is crucial for manufacturers to stay vigilant of the risks and challenges that exist parallel to the benefits.
A strong data and cybersecurity strategy, paired with an advanced IT architecture, regular training, and regulatory compliance, will go a long way in mitigating the hurdles that lay on the path to digital transformation.
If you want more information on digital transformation or how RSM can help you, visit our manufacturing page.
Contributors
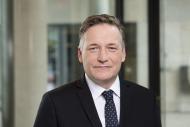