AUTHORS
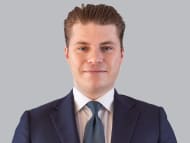
In today's increasingly complex business landscape, the manufacturing industry faces substantial risks related to fraud and corruption. In fact, according to the ACFE’s 2022 ‘Report to the Nations’, businesses lose 5% of revenue to fraud every year.
As trusted advisors to numerous manufacturing organisations, RSM Australia (“RSM”, “we”) recognises the importance of addressing these challenges head-on, utilising the frameworks outlined by the Australian Standard 8001:2021 Fraud and Corruption Control (“AS 8001:2021”), the Committee of Sponsoring Organisation of the Treadway Commission (“COSO”) and Association of Certified Fraud Examiners’ (“ACFE”) joint publication ‘Fraud Risk Management Guide’.
In this article, we explore two significant risks that manufacturers encounter: supply chain fraud risk and bribery and corruption risk in manufacturing. RSM’s team of experienced fraud and forensic specialists provide insights into specific challenges and offer effective strategies to mitigate these risks. By integrating these proactive measures, manufacturers can safeguard their operations, protect their reputation, and ensure long-term, sustainable growth aligned with their strategic objectives.
Supply Chain Fraud - Protecting the Integrity of Manufacturing Processes:
Supply chain fraud poses a significant threat to the manufacturing industry, requiring proactive measures to safeguard operations. Extensive networks of suppliers and vendors, the sheer volume of transactions and global scale makes the manufacturing industry vulnerable to fraudulent activities. RSM recommends the following strategies to mitigate supply chain fraud risks, as aligned with AS 8001:2021:
- Robust supplier due diligence. This is vital to ensure the credibility of business associates. Thorough background checks, financial assessments, and reference verifications help manufacturers assess supplier integrity. Utilising a comprehensive supplier onboarding checklist is a sound starting point before engaging in new business relationships.
- Transparent supplier relationships. Establish clear expectations, maintain open communication channels, and conduct regular internal audits to enhance visibility into the supply chain and strengthen accountability.
- Leveraging advanced technology solutions. Technologies such as blockchain, the Internet of Things (“IoT”) and data analytics enhance supply chain transparency, traceability, and verification, minimising the risk of counterfeit or substandard materials entering the production process.
- Implementing strong internal controls to mitigate supply chain fraud. Segregating duties, implementing robust authorisation processes, regular risk assessments, anti-fraud training, conducting regular internal and external audits, surprise audits (where possible) and enhancing physical and digital security measures are critical steps in safeguarding against supply chain fraud.
Proactive preventative measures coupled with effectively operating detective and corrective controls are critical to maintaining strong control environments, and minimising exposure to supply chain fraud risks. Engaging with your trusted advisor to conduct a health check of your control environment is an important first step in combatting fraud risk.
Bribery and Corruption - Nurturing a Culture of Ethical Conduct:
Bribery and corruption risks can significantly impact the manufacturing sector, requiring a proactive and holistic approach. Although often used interchangeably, it is important to distinguish between Bribery and corruption risks and Fraud Risks.
Bribery and corruption encompasses a range of risks, including conflicts of interest, kickbacks, bid rigging, illegal gratuities and economic extortion. This is distinct from Fraud risks, which often include asset misappropriate and financial statement fraud. RSM recommends the following strategies to address bribery and corruption risks:
- Implementing comprehensive anti-bribery and corruption policies and governance frameworks is fundamental. These policies and governance frameworks should align with better practice such as AS 8001:2021, define acceptable behaviour, and establish consequences for non-compliance.
- Fit for purpose fraud training and awareness programs. Educating employees and stakeholders about the risks of bribery and corruption fosters a culture of ethical conduct. Fraud training and awareness programs should set the ‘Tone at the Top’ and provide guidance on recognising and reporting suspicious activities as well as how confidential whistleblower hotlines (if available) are operationalised in the business. Comprehensive and tailored fraud training programmes increase the perception of Bribery and corruption detection. Increasing the perception of detection is one of the most effective internal controls to combat Bribery and Corruption.
- Strong internal controls, monitoring and reporting mechanisms. Effectively designed and operating internal controls are crucial in mitigating bribery and corruption risks. Regular audits, bribery and corruption risk assessments, independent reviews and investigations, and robust monitoring and reporting ensure the early detection of red flags.
- Foreign bribery and corruption risk (or often called Anti-Bribery and Anti-Corruption or “ABAC”) consideration. If your business conducts business internationally (including has a business entity in an oversea location(s), imports or exports, or uses agents of intermediaries to do business), you may be captured by foreign bribery and corruption legislation with differing requirements country to country and some legislation that has global reach (e.g. the Australian Commonwealth Criminal Code Act 1995, the US Foreign Corruption Practices (“FCPA”) 1977, or the UK Bribery Act 2010) there may be legislative requirements and there are mitigation better practices (e.g. the international standard ISO 37001 Anti-Bribery Systems) that businesses can utilise in mitigating these risks.
RSM encourages collaboration with industry peers and relevant authorities. Engaging with your trusted advisor and industry associations, such as the ACFE and COSO, and sharing best practices helps manufacturers stay ahead of emerging risks and combat bribery and corruption collectively.
In a rapidly evolving business environment, addressing supply chain fraud and bribery and corruption risks is paramount for the manufacturing industry. RSM's team of experienced fraud and forensic specialists highlight the importance of implementing robust measures, including thorough supplier due diligence, advanced technology solutions, nurturing a culture of ethical conduct, and strengthening internal controls.
By integrating these proactive strategies, manufacturers can safeguard their operations. Effective governance processes are the foundation of fraud risk management, and the lack of effective corporate governance seriously undermines any fraud risk management program.
FOR MORE INFORMATION
Please contact our RSM’s Fraud & Forensic Services team today for a complimentary and confidential consultation.
Article source: Manufacturer's Monthly